I finally got back to working on the Panda + improvements during rebuild+refurbish the Panda. It is almost ready for primer. While probably not necessary, since I am having to do a partial rebuild, I might as well make improvements.
Changes so far:
- Increased overall height of tube portion of electronics bay by 10mm on top. This decreases the size of the coupler+bulkhead extension up into the nosecone thereby increasing the volume for the shock cord and drogue chute, making it a less tight fit. While the previous design caused no issues on the last flight, it made drogue chute packing tedious and accident prone.
- Increased overall height of tube portion of electronics bay by 18mm on bottom. When the nose deployed early, this was the failure point separating the rocket into two pieces. I know that all is probably fine with this joint, but if I'm rebuilding it, having some extra surface area for the coupler/bulkhead increases structure strength tremendously.
- I've tested radio frequencies passing through when printing using carbon fiber polycarbonate (CF/PC). To properly test, I had to make sure there is no loss of radio signal since it does contain carbon fibers. I've tested 900mhz, GPS, cell signal and they all pass through without loss. The fibers must not be dense enough to inhibit signal. The specific brand has of CF/PC has nice specifications and printed parts are very strong: #^https://www.3dxtech.com/product/carbonx-pc-cf/
- While I had no problems with strength of bay, by using CF/PC the bay will be significantly stronger and lighter. I'll still wrap it in a few layers of 2oz glass on the outside, and a few strips of glass on the interior surface making it a nice sandwich. Sandwiching 3d print significantly increases the lifespan of the 3d print as joints have additional bonding by the glass and can't separate over time.
- Lower coupler and bulkhead has been increased in thickness by 1.5mm and is now a min. thickness of 3.5mm. Top of coupler reaches into bay piece by 8mm more for a total of 22mm. Bulkhead has been moved down 16mm allowing for more storage of wiring. Total coupler length is now 7cm.
- I'll create a kevlar loop around the electronics bay with the intent to keep the entire rocket together. On the first launch, this was the first rocket where I did not create a loop due to strength in bay and coupler/bulkhead components - a mistake.
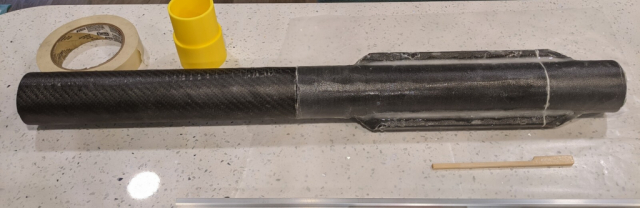
The left half is 5.7oz/sq yd solid carbon fiber twill rolled laminations as it is just body tube. The CF is sandwiched on both sides by a wrap of 2oz fiberglass to smooth & make it easier to work with.
The right half is printed CF PC wrapped twice in 2oz/sq yd fiberglass. The fillets are standard epoxy with an add of colloidal silica filler.
As always, this will be smooth when complete, with a nice paint finish. While the previous airframe was very strong, this version brings it to a whole new level.
Repairing the fincan is much easier, I'll post some photos of that once I spend more time on it.
Rocketry (software + hardware + fabrication) is a hobby, not my job. It is probably a hobby I spend way too much time at, but I really enjoy the hobby and the complex problems that have to be solved.